9 Steps To Making Awesome Vinyl Records
- Scott Hull
- Feb 13, 2023
- 6 min read
Updated: Mar 23, 2023
Advice from our vinyl guru, Scott Hull
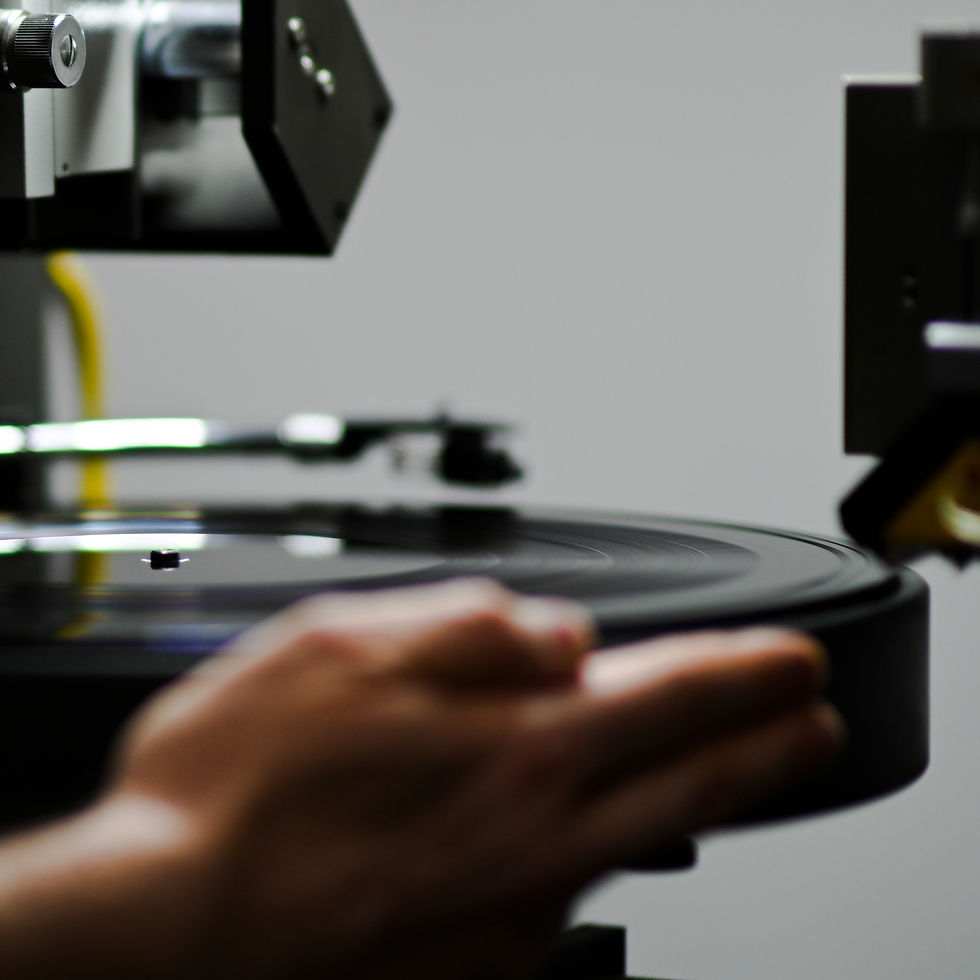
Vinyl is BOOMING. It’s made an unexpected resurgence in the last ten years, with its popularity only growing more and more. However, because of the interim decades when vinyl production was at an all-time low, certain aspects of the process of mastering for vinyl and cutting the record itself have become somewhat mystifying.
Our own Scott Hull, owner and chief mastering engineer here at Masterdisk, began his career when vinyl was still king. Over the years, he developed a sage-like wisdom about the now-mysterious art. Here are nine things you need to know about the process of cutting a record that will make your mind melt.
1. Mastering For Vinyl
When you want to craft a record of titanic tuneage, you have to create a master that is made specifically for vinyl. The process is similar to creating a master for CDs, but with its own quirks. The mastering engineer must be aware of the differences between mastering for different mediums. Even when this noble craft is honed, you need a studio that is specifically equipped for working with vinyl. When your mastered tunes, or the “cutting master,” are ready, they’ll be sent to you for approval as .WAV files.
2. Cutting The Record
Once you have an approved cutting master, Scott takes your project to the lathe for further evaluation and contemplation. Once all the cutting parameters have been tested and the cut is to Scott’s satisfaction, a reference disc is cut on a lacquer disc that looks just like a normal record.
Ok, there are some common misconceptions here: many cutting engineers feel that they have to reduce the bass and soften the high frequencies to make it work. Not so awesome. Except in some rare circumstances, it is possible to transfer all of the sounds to the disk. Awesome, right? With the best gear–and patience–the best engineers, like Scott, are able to make your record sound exactly like your vinyl-cutting master.
3. Quality Control
After the reference disk is cut, Scott listens to it on a turntable. A trained ear will listen for distortion, skips or overcuts, excessive noise floor, and any issues with tracking or disturbances in the playback. This is called quality control, and it ensures nothing gets in the way of your righteous tuneage. It can be done in-house by the mastering engineer, and often, reference disks are cut and sent to the artist or producer so their ears may confirm the awesomeness of quality.
4. Approval of the Reference Disks
When the reference disk passes quality control (the cool kids call it QC), the mastering engineer, the producer, and the artist all listen and comment on the record to give their impressions. Adjustments are made based on those comments and impressions, and, if necessary, another reference lacquer will be cut for approval.
5. Cutting Master The Lacquers
This is the “master” copy of the record that will be delivered to your chosen plating and pressing company. Be wary, for master lacquers cannot be played without damaging the disc. We cut the music onto a lacquer, a record-like disk. It has an aluminum base plate, attached to which is about 20 millimeters of soft lacquer—think: very thin, dark-purple paint. It’s dry to the touch but can easily be indented by a fingernail. Lacquers cut as masters should not be played because they are soft, and even a careful needle drop will cause a very loud pop on every copy of the record. One must be very careful to document the settings from the reference disc in order to repeat them precisely after it's approved. It’s like sonic surgery, and precision is paramount.
6. Plating
This is where things start to get metal. When the master lacquer is finished, it is bolted into a specially constructed box and carefully and quickly shipped to a facility where plating begins, and metal parts are made. Generally, the master lacquer is sprayed with silver nitrate and then electroplated with nickel. The metal is then separated from the master lacquer, which reveals a kind of “negative” of the master, with outward protrusions that match the groove of the master exactly.
7. Mothers and Fathers
The first metal “part” that is pulled off the lacquer is a “negative” of the master, and it is called the Father. After this initial plate is made, it is then plated again. The Second metal part that is pulled off the father is called the Mother, and it has normal grooves like a record. It looks awesome; your songs are actually cast in metal! The mother is then plated, and this third plate is called the stamper. These stampers are placed into the record press, which birth the masses of records for your fans to buy.
8. Test Pressings and Production Runs
Before your hit record makes its first production run, test pressings of the record are made, which are, in turn, sent back to you for thumbs up. Once approved, a production run is made, and the record is assembled and shipped. Then boxes and boxes of records show up, and you must figure out where to put them!
For very short runs, you can skip the mother and father steps above and use that first plate as your stamper. There won’t be any loss in quality, but you will be limited to only the number of records that can be pressed before the stamper breaks–and they do break! Typically this is recommended for only runs of under 150 disks. This could be called a “one-step process,” as opposed to the two and three-step processes involving the mother and father plates. You can’t easily re-order more copies if you go the one-process route, and you’d have to pay for a new master lacquer and new plates.
9. How to Listen to Test Pressings
To ensure that your record is at the height of ear-melting enormity, you must ensure the test pressings check out. Test pressings aren’t perfect. Even when everything else in the process is done perfectly, sometimes test pressings will have some flaws anyway. Only a trained ear can tell the difference between serious defects in the process and ordinary flaws that are associated with the test pressings themselves. It’s strongly recommended that you send a couple of these test pressings to your cutting studio for review. Your cutting engineer (in this case, Scott), is the only person who knows how your test pressing should sound. You’ll still want to listen to them yourself because you’re awesome. So, when you get your test pressings, what are you supposed to listen for?
Any major flaw that would ruin the record, like skips, and locked grooves (repeats).
Other audible flaws that would detract from the listening experience. Once around or swishing sounds, harshness and excessive high-frequency distortion called sibilants.
Surface flaws that may be annoying and may be part of the process. Clicks and pops: small ones are normal, but really loud ones that are plainly audible need to be investigated.
Oh yeah, and don’t forget to check the running order, gaps and any inscriptions in the “dead wax.”
All test pressings have noises. Making a super short run on a manual press is just going to be noisy because they are not often made in ideal conditions. There are several reasons for this: It’s a different press, the temperature might not be optimal, and the quality of the vinyl may not be the same as they will use for your final run. So don’t go too crazy over it.
Your final records should be quieter than your test pressings. But there is a catch, and this is why you want more than just one or two test pressings available: if a noise—even a loud pop–is not audible on every test pressing, then the stamper is likely good, and the process can be continued. But, if that noise is on every test pressing, then the plant should be contacted, alerted to a potential flaw in the stamper, and you should await their reply.
For Your Consideration:
As you’ve seen, there’s plenty that could go wrong in the process of cutting a record; because of this, make sure you put in that extra effort to collaborate with people who are known for quality. There’s an old saying that’s been passed down from the great Bob Ludwig: “Perfect is close enough.”
One of the hard truths is that spending enough money and time is one of the big requirements for making a great record. If you're setting out to make an inexpensive record, that's okay, but you can't expect that to be an amazing piece of vinyl. A poorly cut record will not only have defects that detract from the music, but it will also be boring to listen to (imagine your music with the bass control turned down and the tweeters covered with a sweater). That is what a cheaply cut record sounds like.
Keep this in the front of your mind: knowing your audience is really important. Are these audiophiles who are buying the record because they love the sound of vinyl? In that case, it'd be kind of silly to make them a cheap record — they could get turned off from your project as opposed to being turned on by it. But if it's for the 7" crowd and all about the attitude and the vibe, you might be wasting your production money on a really precise cut and pressing.
Here’s the main squeeze: the cut is important. If you don't start with a good groove, it doesn't matter how you plate or press it; it will be noisy. If you have to cut corners by using a less expensive pressing facility, then you may want to make sure it gets cut well, at a good hot level, because that will help you beat the noise floor.
コメント